Hello again everyone! The behind the scenes look continues, and now we’re getting to the messy bits!
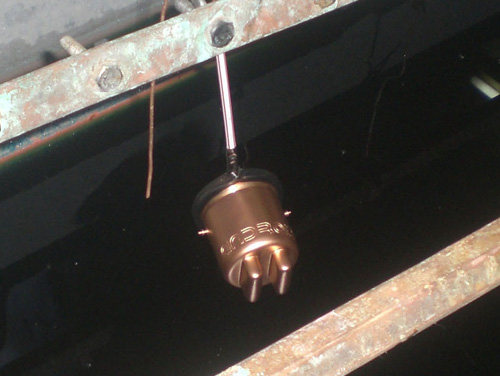
Multiple copies of the a metal molds are created from the original master mold.
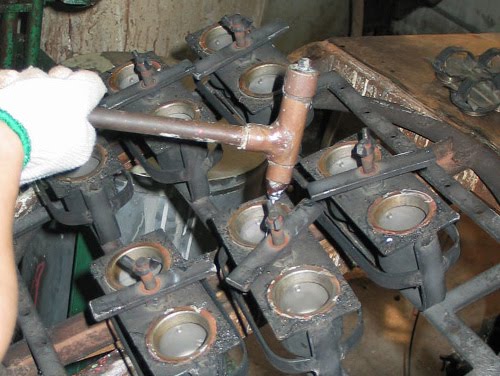
These molds are then attached to a frame built specifically for a roto-casting (aka rotational casting) machine. These particular frames pictured hold 12 android body molds. Hot liquid vinyl is poured into each form on the frame.
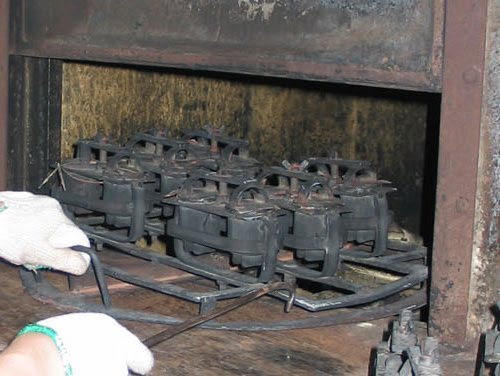
The molds are then capped off and inserted into a large roto-casting machine. This machine is essentially a large oven that spins the molds around in different directions while they bake. By spinning the molds we can ensure that the liquid vinyl coats all of the inside surfaces of the molds evenly and fully. Rotocasting also requires far less material than solid molding, and results in a lighter and more flexible product.
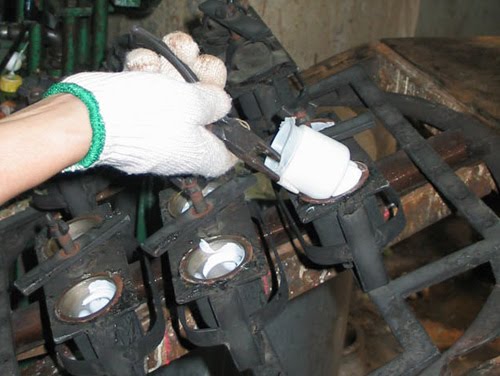
After a quick cool-down, the raw forms are still warm and soft enough to easily be pulled out of their molds. The excess material around the seams is trimmed off.
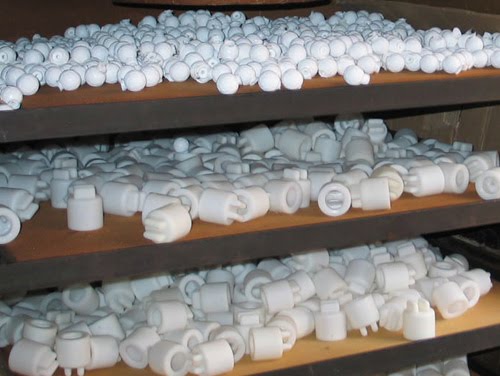
Sometimes the figures will become somewhat warped when they are pulled out of the molds. A quick trip to a heating rack makes them pop back into their original heat-formed shape.
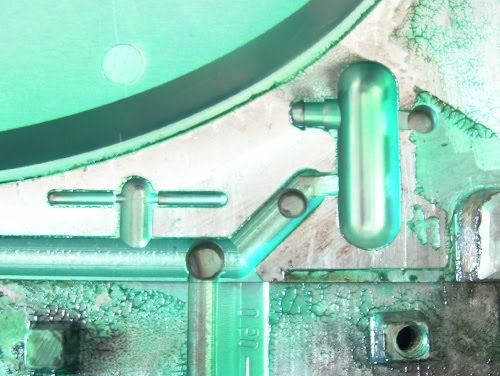
Arms and antennae are too small and precise to be rotationally molded, those are created by a process called injection molding. Here the material is injected under extreme heat and pressure into a two part mold made from a solid aluminum block. Here you can see half the antennae on the left and half an arm on the right. That “gunk” you see helps lubricate the mold and ensure a good solid seal between the two parts.
Next Time: Painting pretty colors!